Understanding and Preventing Die Casting Defects
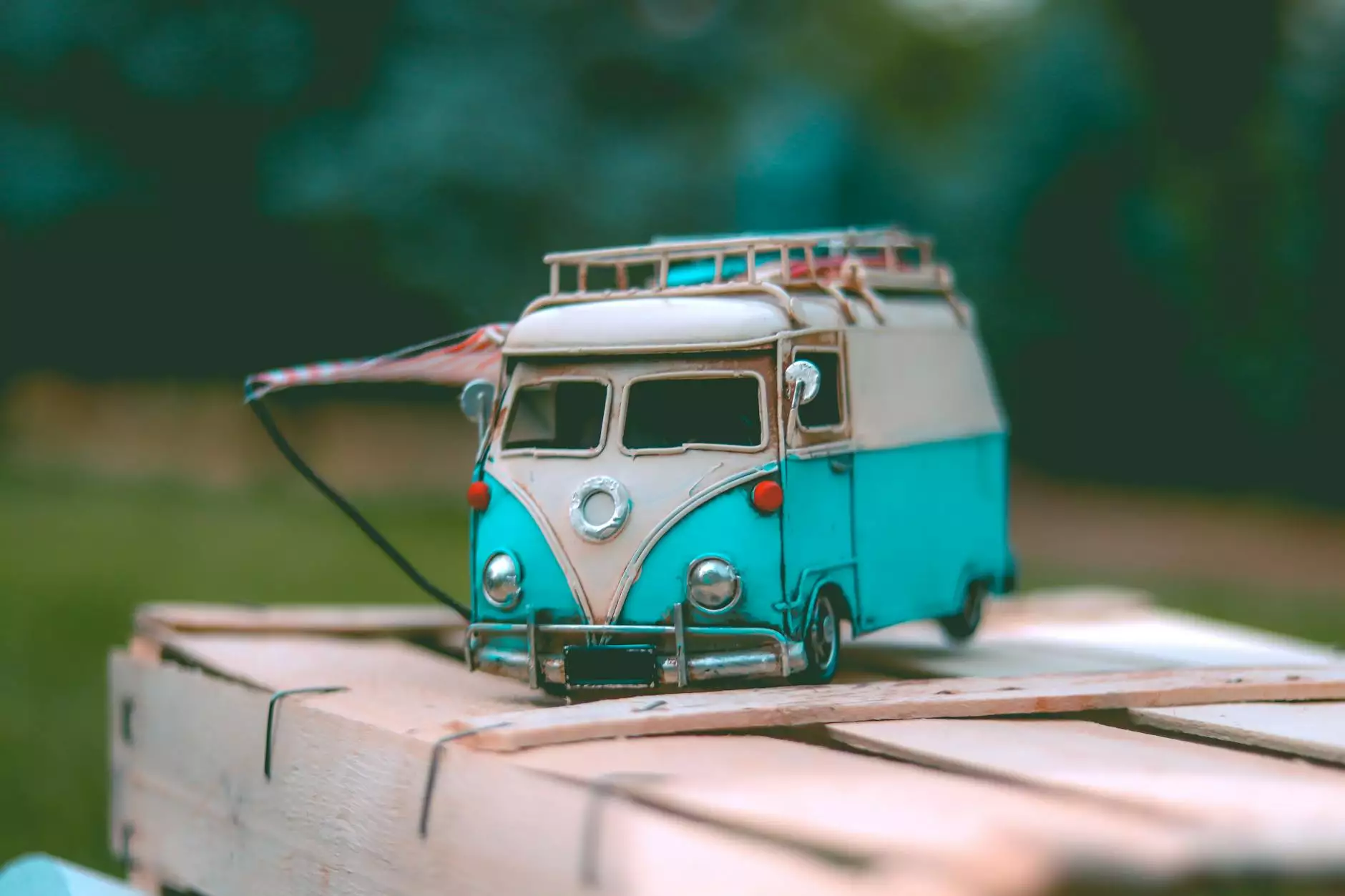
Introduction
Welcome to Wetron Industrial, your trusted provider of top-notch home and garden appliances. In this article, we will delve into the world of die casting defects and explore effective methods to prevent them. With our extensive knowledge and expertise, we aim to provide you with valuable insights to optimize your die casting processes and achieve outstanding results.
What are Die Casting Defects?
Die casting is a common manufacturing process used to produce complex and durable metal components. However, like any process, it can be susceptible to certain defects that may compromise the final product's quality.
Porosity
Porosity is a commonly encountered defect in die casting. It refers to the presence of small voids or cavities within the cast part. These voids can weaken the structural integrity of the component and lead to its failure. To prevent porosity, several measures can be taken. Proper gating and venting system design, controlling the melt temperature and flow rate, and utilizing suitable die lubricants are a few key considerations.
Blistering and Air Entrapment
Blistering and air entrapment are defects that result in the formation of raised areas or bubbles on the surface of cast parts. These defects are often caused by the presence of trapped air or gas within the molten metal during the casting process. To minimize the occurrence of blistering and air entrapment, implementing appropriate degassing techniques, optimizing the die temperature, and ensuring proper die venting are crucial steps.
Cold Shut
Cold shut refers to a defect characterized by an incomplete fusion of two or more molten metal fronts during solidification. It appears as a visible line or seam on the cast part's surface. This defect is typically caused by insufficient molten metal temperature or poor gate and runner design. To prevent cold shut, maintaining proper metal temperature, enhancing gating system design, and optimizing the filling process are vital.
Uneven Shrinkage
Uneven shrinkage is a defect that occurs due to non-uniform cooling and solidification of the molten metal. It results in uneven dimensions and distortions in the final part. This defect can be minimized by carefully controlling the cooling rate, utilizing proper cooling channels in the die, and optimizing the alloy composition to enhance its solidification characteristics.
Preventing Die Casting Defects
While die casting defects can pose challenges, implementing appropriate preventive measures can significantly reduce their occurrence. To ensure high-quality cast parts, consider the following recommendations:
Use High-Quality Die Materials
The choice of die materials plays a crucial role in determining the success of the die casting process. Opt for high-quality dies that withstand high temperatures and offer excellent thermal conductivity. This helps maintain consistent and controlled temperature conditions during casting.
Maintain Optimal Operating Parameters
Controlling process parameters such as die temperature, molten metal temperature, pressure, and cooling rate is paramount. Strict monitoring and adherence to optimal operating parameters can minimize defects and ensure consistent casting quality.
Implement Effective Die Lubrication
Proper die lubrication is crucial for preventing defects and prolonging the die's lifespan. It helps enhance metal flow, reduce friction, and prevent sticking. Utilize high-quality die lubricants and establish a regular lubrication schedule to ensure efficient die performance.
Invest in Advanced Casting Simulation
Casting simulation software can provide valuable insights into the die casting process before actual production. It enables you to identify potential defects, optimize gating design, simulate metal flow, and make informed decisions to enhance casting quality.
Regular Maintenance and Die Inspections
Frequent die maintenance and inspections are key to preventing defects. Regularly clean and inspect dies to identify signs of wear, damage, or any potential issues. Timely repairs and replacements can significantly improve casting performance and reduce the risk of defects.
Conclusion
Die casting defects can pose challenges in achieving high-quality metal components. However, by understanding the common defects and implementing preventive measures, you can significantly enhance your casting processes. At Wetron Industrial, we strive to provide exceptional home and garden appliances that assist you in achieving outstanding results. For all your appliance needs, visit our website on www.wetronindustrial.com.