Molding Car Parts: Revolutionizing the Automotive Industry
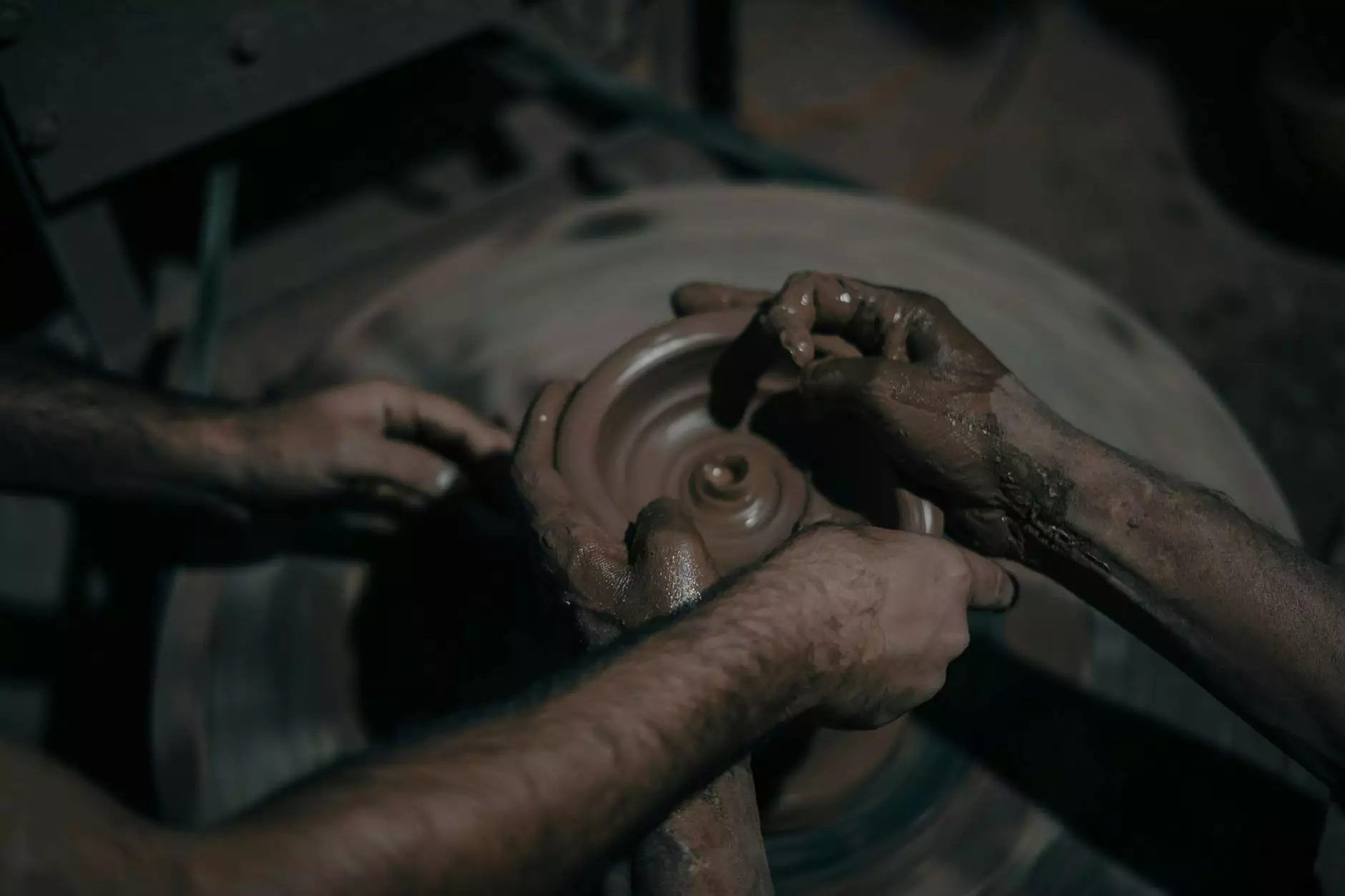
The automotive industry is undergoing a significant transformation, driven by innovation, technology, and a growing demand for efficiency. One of the most critical aspects of this revolution is molding car parts. This process not only enhances the quality and design of vehicles but also contributes to a more sustainable environment. In this comprehensive article, we will explore the various facets of molding car parts, including the benefits, processes, and innovations that make it a cornerstone of modern automotive manufacturing.
Understanding Molding Car Parts
At its core, molding car parts refers to the manufacturing technique used to create components for vehicles through various molding processes. These methods include:
- Plastic Injection Molding: A process where molten plastic is injected into a mold to form specific shapes.
- Blow Molding: Used primarily for making hollow parts, where air is blown into heated plastic to create designs.
- Compression Molding: Involves placing a preheated plastic material in a mold and applying pressure to form the part.
Each of these techniques plays an integral role in manufacturing high-quality car components that are lightweight, durable, and cost-effective. Hanking Mould, a leading manufacturer in the industry, specializes in producing plastic molds for various automotive applications, ensuring that every product meets stringent industry standards.
The Benefits of Molding Car Parts
The benefits of adopting molding processes for producing car parts are manifold. Here are some key advantages:
1. Cost-Effectiveness
Using molding techniques can significantly lower production costs. The initial investment in molds may be high, but they can produce thousands of identical parts with minimal labor and material waste. This efficiency translates into lower costs per unit, making automotive manufacturing more economically viable.
2. Design Flexibility
Molding processes allow for complex designs that would be challenging to achieve with traditional manufacturing methods. Designers can create intricate shapes, reducing the need for assembly and improving the overall aesthetics of the vehicle.
3. Material Efficiency
With molding, materials are utilized more effectively, minimizing waste. The precision of plastic injection molding allows manufacturers to achieve high production yields, utilizing the full potential of the raw material.
4. Durability and Lightweight
Molded car parts are typically lighter than their metal counterparts, enhancing the fuel efficiency of vehicles. Furthermore, the durability of modern plastics helps ensure that these components can withstand harsh environmental conditions, contributing to the longevity of the automotive parts.
5. Sustainability
As the automotive industry shifts towards more sustainable practices, molding processes offer eco-friendly solutions. Many plastic materials used in molding are recyclable, and advancements in bioplastics offer even more environmentally friendly options.
Key Processes in Molding Car Parts
Understanding the specific processes involved in molding car parts is crucial for any automotive manufacturer. Let's dive deeper into these methods:
Plastic Injection Molding
This is one of the most common techniques for producing molded car parts. The process involves heating plastic pellets until they melt, then injecting the molten plastic into a precisely designed mold under high pressure. The benefits of plastic injection molding include:
- High Production Rates: Capable of producing large quantities of parts quickly.
- Precision: Enables the manufacturing of complex geometries and tight tolerances.
- Reduced Labor Costs: Automation in the injection molding machine reduces the need for manual intervention.
Blow Molding
This technique is mainly used for creating hollow parts, such as fuel tanks and various fluid containers. In blow molding, a tube of hot plastic, known as a parison, is inflated to fill a mold. The benefits include:
- Versatility: Suitable for a variety of materials and shapes.
- Efficiency: Quick cycle times due to the rapid inflation process.
Compression Molding
Compression molding is particularly useful for thermosetting plastics, where the material is heated, placed in a mold, and then compressed. This method is ideal for larger parts and components that require a high degree of strength. Key advantages include:
- Cost-Effective for Large Parts: Although the cycle time is longer, it is often cheaper for larger components.
- Reduced Waste: Material is contained within the mold area, minimizing excess.
Innovations in Molding Car Parts
The automotive industry is consistently evolving, driven by technological advancements. Recent innovations in molding car parts include:
1. Advanced Materials
New materials, such as composite and biodegradable plastics, are being developed to improve the performance and sustainability of molded car parts. These materials can offer enhanced strength-to-weight ratios, contributing to the overall efficiency of vehicles.
2. 3D Printing
3D printing technology is making waves in prototype development and small-batch production of car parts. This technology allows for rapid prototyping, enabling manufacturers to test designs before committing to high-volume production.
3. Smart Molding Techniques
Integration of sensors and automation into molding processes allows for real-time monitoring and adjustments, leading to higher quality and reduced waste. Smart factories are becoming a reality as industry 4.0 technologies penetrate the automotive manufacturing landscape.
Challenges in Molding Car Parts
While the benefits of molding car parts are substantial, several challenges must be addressed:
1. Investment Costs
The initial investment in molds and machinery can be high, which may deter small manufacturers from pursuing this method. However, as production ramps up, the long-term savings usually outweigh the initial costs.
2. Technical Expertise
Molding car parts requires specialized knowledge in material properties, mold design, and process optimization. Manufacturers must continually invest in training and development to keep their workforce skilled and knowledgeable.
3. Sustainability Concerns
While many plastics are recyclable, the overall environmental impact of plastic production remains a concern. The industry must focus on developing more eco-friendly materials and processes to address these concerns effectively.
The Future of Molding Car Parts
As the automotive industry continues to evolve, the future of molding car parts looks promising. With advancements in technology and growing environmental awareness, manufacturers are adopting innovative practices to stay competitive. Key trends include:
- Increased Use of Recyclable Materials: Focused efforts on using sustainable materials will shape the future production processes.
- Greater Automation and Efficiency: Enhanced automation techniques will improve process efficiency and reduce the labor involved in manufacturing.
- Customization and Personalization: Consumers are seeking unique and personalized vehicles, driving the demand for customized car parts.
In conclusion, molding car parts represents a revolutionary step forward in automotive manufacturing. With benefits that encompass cost-effectiveness, design flexibility, and sustainability, it is clear that this technique is not just a trend but a necessity for the future of the industry. Hanking Mould continues to lead in this sector, offering advanced solutions in plastic mold making and injection molding that cater to the evolving needs of the market. As technology continues to advance and consumer preferences shift, the importance of molding car parts will only grow.
For more information about our services in plastic mold making and plastic injection mould manufacturing, visit us at hanking-mould.com.